Discover the impact of RTV conductive thermal adhesives and RTV silicone sealants on modern manufacturing. Learn about their specifications, applications, storage guidelines, safety measures, and why Electo is the trusted choice for leading industries.
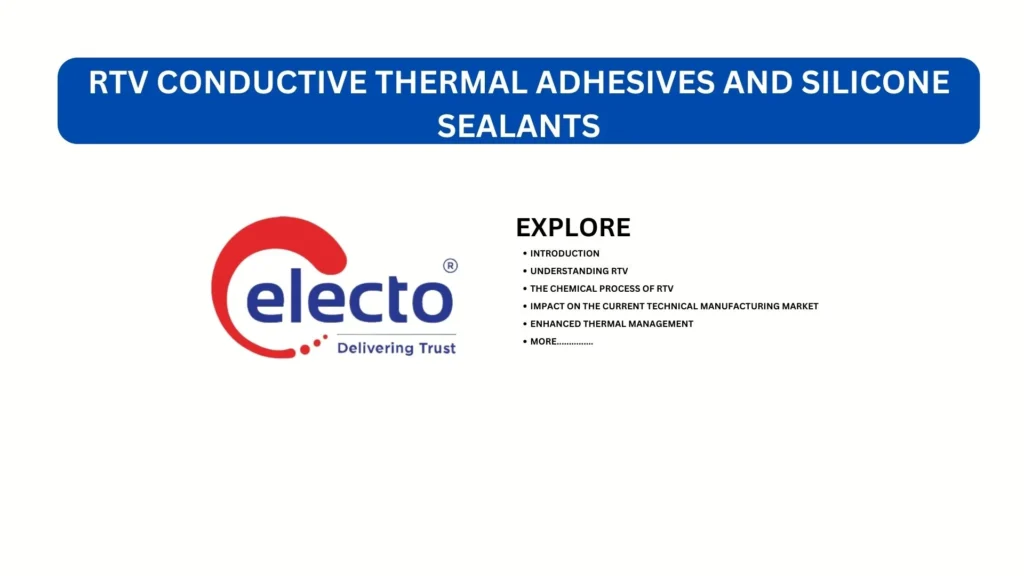
In an era of unprecedented technological advancement, the demand for high-performance materials has never been greater. From the intricate circuitry of electronic devices to the robust components of automotive engines, the need for reliable, efficient, and versatile materials is paramount. Enter RTV (Room Temperature Vulcanizing) conductive thermal adhesives and RTV silicone sealants—two groundbreaking solutions that have transformed various industries with their exceptional properties. This comprehensive guide will walk you through the world of RTV materials, exploring their impact on modern manufacturing, their specifications, applications, and much more. Join us as we delve into why RTV adhesives and sealants are indispensable in today’s high-tech world and discover how our brand, Electo, is at the forefront of delivering trusted, high-quality products to leading industries worldwide.
introduction
In today’s rapidly advancing technological landscape, where exceptional performance and reliability are paramount, the emergence of RTV (Room Temperature Vulcanizing) conductive thermal adhesives and RTV silicone sealants has been transformative across various industries. From electronics to automotive manufacturing, these materials have become indispensable components. This blog aims to delve into the essence of RTV, elucidating its profound impact on the current technical manufacturing market. We will navigate through a detailed comparison between RTV and standard thermal adhesives and sealants, highlighting their distinctive attributes. Furthermore, we will explore the extensive applications and industries served by RTV, emphasizing its versatility and adaptability in diverse settings. Additionally, we’ll address the importance of adhering to proper storage guidelines and safety measures when handling RTV materials, ensuring optimal performance and user safety. Understanding the significance of selecting the right thermal adhesives will also be underscored, elucidating its implications for product integrity and efficiency. Lastly, we’ll shine a spotlight on Electo’s offerings, elucidating why our brand’s products are trusted by leading industries worldwide, owing to their unmatched quality, innovation, and customer support.
Understanding RTV
RTV, which stands for Room Temperature Vulcanizing, refers to a category of silicones renowned for their unique curing process at ambient temperatures. RTV silicones exhibit exceptional flexibility, durability, and resistance to a myriad of environmental stressors, including moisture, chemicals, and extreme temperatures. This distinctive combination of properties renders RTV silicones indispensable across a broad spectrum of applications, particularly in environments where traditional materials might falter. Whether used in electronics for encapsulating delicate components, automotive applications for sealing critical components against harsh conditions, or in construction for weatherproofing and sealing joints, RTV silicones offer unmatched versatility and reliability. Their ability to form resilient seals and bonds while maintaining flexibility enables them to withstand thermal expansion, mechanical stress, and chemical exposure without compromising performance. From aerospace to healthcare industries, RTV silicones continue to be favored for their ability to provide durable, long-lasting solutions in demanding environments, making them an indispensable choice for engineers and manufacturers seeking reliable and adaptable materials.
The Chemical Process of RTV
The vulcanization process in RTV silicones is a chemical transformation where polymer chains form cross-links, creating a stable and robust structure. This process, often catalyzed by moisture in the air, is one of the defining features of RTV silicones, making them exceptionally convenient and user-friendly. Unlike other sealants and adhesives that may require additional curing agents or external heat sources to initiate and complete the curing process, RTV silicones cure at room temperature simply through exposure to atmospheric moisture. This inherent property not only simplifies the application process but also reduces the need for specialized equipment and additional energy input, making it highly efficient and cost-effective. The resulting vulcanized silicone retains its flexibility and resilience over a wide temperature range, from extreme cold to intense heat, ensuring consistent performance in diverse conditions. Furthermore, RTV silicones exhibit excellent adhesion to a variety of substrates, including metals, plastics, glass, and ceramics, making them versatile for numerous industrial applications. Their ability to form durable, elastic bonds that resist environmental degradation, mechanical stress, and chemical exposure underscores their importance in sectors such as electronics, automotive, aerospace, and construction, where reliability and longevity are paramount.
Impact on the Current Technical Manufacturing Market
The advent of RTV conductive thermal adhesives and RTV silicone sealants has revolutionized the technical manufacturing market, providing unparalleled solutions in thermal management, electrical insulation, and sealing applications. These advanced materials are engineered to meet the rigorous demands of high-tech industries, offering superior performance that has become indispensable in the production of electronic devices, automotive parts, aerospace components, and medical devices. One of the standout features of RTV materials is their ability to cure at room temperature, which significantly simplifies the manufacturing process. This room temperature vulcanization (RTV) eliminates the need for high-temperature curing ovens, thereby reducing energy costs and streamlining production workflows. Additionally, the exceptional thermal conductivity of RTV conductive adhesives ensures efficient heat dissipation from electronic components, preventing overheating and enhancing device longevity. Concurrently, RTV silicone sealants provide robust electrical insulation, crucial for safeguarding sensitive electronic assemblies from electrical shorts and environmental contaminants. Their versatile sealing capabilities also ensure durability and reliability in harsh conditions, from automotive engines to aerospace applications. Consequently, the integration of RTV materials into manufacturing processes has not only enhanced product performance and reliability but also increased production efficiency and cost-effectiveness, making them vital components in contemporary technical manufacturing.
Enhanced Thermal Management
RTV conductive thermal adhesives are pivotal in the realm of thermal management, particularly in electronic devices where efficient heat dissipation is critical. These adhesives are engineered to facilitate the transfer of heat away from high-power components such as CPUs and GPUs, which generate significant amounts of heat during operation. By effectively dissipating this heat, RTV conductive thermal adhesives help maintain a stable temperature within electronic assemblies, thereby preventing overheating that could lead to performance degradation or even irreversible damage. In high-power applications, where components operate at intense workloads, the role of thermal management becomes even more crucial. RTV conductive thermal adhesives ensure that the heat generated is rapidly and efficiently transferred to heat sinks or other cooling solutions, thereby maintaining the optimal operating conditions of the devices. This not only enhances the performance and reliability of the components but also extends their operational lifespan. The ability of these adhesives to withstand thermal cycling and maintain strong adhesive bonds under varying temperatures further underscores their importance in ensuring the safety and efficiency of electronic systems. Thus, RTV conductive thermal adhesives are indispensable in the design and maintenance of high-performance electronic devices, contributing significantly to their durability and optimal functioning.
Improved Electrical Insulation
RTV silicone sealants are highly valued in the electronics industry for their exceptional electrical insulation properties, making them indispensable for a variety of electronic assemblies and applications requiring electrical isolation. These sealants provide robust insulation that can withstand high voltages, ensuring that electronic components remain protected from electrical shorts and potential breakdowns. This high resistance to electrical conductivity prevents unwanted current flow, which is critical in maintaining the integrity and functionality of sensitive electronic circuits. Additionally, RTV silicone sealants maintain their insulating properties over a wide range of temperatures and environmental conditions, from the extreme cold to intense heat, ensuring consistent performance in diverse applications. Their inherent flexibility allows them to absorb mechanical stress and thermal expansion, preventing damage to delicate components and connections. Furthermore, RTV silicone sealants’ resistance to moisture and environmental contaminants further enhances their insulating capabilities, protecting electronic assemblies from potential corrosion and degradation. This reliability and durability in providing electrical isolation make RTV silicone sealants a preferred choice for engineers and manufacturers aiming to safeguard the performance and longevity of electronic devices, ranging from consumer electronics to critical aerospace and automotive systems.
Robust Sealing Solutions
The sealing properties of RTV silicone sealants are unmatched. They provide a strong, flexible seal that can withstand extreme temperatures, moisture, and chemical exposure. This makes them perfect for sealing applications in automotive engines, aerospace components, and industrial machinery. RTV silicone sealants are renowned for their superior sealing properties, providing a robust and flexible barrier that can endure extreme conditions. These sealants excel in applications where traditional materials might fail, such as in automotive engines, aerospace components, and industrial machinery. Their ability to withstand a wide temperature range—from the freezing cold to scorching heat—ensures that seals remain intact and effective, even in the most demanding environments. Moreover, RTV silicone sealants offer exceptional resistance to moisture, preventing water ingress and corrosion, which is crucial for maintaining the integrity of engine gaskets, aircraft assemblies, and industrial equipment. Their chemical resistance further enhances their durability, allowing them to maintain their sealing properties despite exposure to oils, fuels, and other harsh chemicals. This resilience makes RTV silicone sealants an indispensable choice for industries where reliability and performance are paramount. By providing a consistent and long-lasting seal, they help prevent leaks, enhance safety, and reduce maintenance costs. Their versatility and dependability make them a preferred solution for engineers and manufacturers aiming to ensure the longevity and efficiency of critical components and systems.
Specifications of RTV Conductive Thermal Adhesives and RTV Silicone Sealants
RTV conductive thermal adhesives and RTV silicone sealants are engineered with specific properties that render them indispensable for a wide array of high-performance applications. These materials offer a unique combination of attributes, making them suitable for demanding environments where reliability, durability, and versatility are paramount. RTV conductive thermal adhesives are formulated with high thermal conductivity, ensuring efficient heat dissipation from electronic components such as CPUs and GPUs. This property is crucial for preventing overheating and ensuring the longevity of devices, particularly in high-power applications. Additionally, these adhesives exhibit excellent adhesion to various substrates, including metals, ceramics, and plastics, providing strong and durable bonds essential for reliable performance. On the other hand, RTV silicone sealants boast exceptional flexibility, durability, and resistance to environmental factors such as moisture, chemicals, and extreme temperatures. This makes them ideal for sealing applications in automotive engines, aerospace components, and industrial machinery, where traditional materials might fail. Understanding the specifications of RTV materials is paramount for selecting the right material for specific applications, ensuring optimal performance, reliability, and safety of products across industries.
RTV Conductive Thermal Adhesives
- Thermal Conductivity: Typically ranging from 1.0 to 5.0 W/m·K. This high thermal conductivity ensures efficient heat transfer away from electronic components.
- Curing Time: Can vary from minutes to hours, depending on the formulation and environmental conditions. Faster curing times can enhance production efficiency.
- Operating Temperature Range: -50°C to 200°C. This wide temperature range allows these adhesives to perform reliably in extreme conditions.
- Electrical Conductivity: Low to high, depending on the specific application. Some formulations are designed to be electrically conductive, while others are electrically insulating.
Thermal Conductivity
RTV silicone adhesives offer thermal conductivity typically ranging from 1.0 to 5.0 W/m·K. This property ensures efficient heat dissipation from electronic components, crucial for maintaining optimal performance and preventing overheating. High thermal conductivity facilitates the transfer of heat away from sensitive parts, thereby enhancing the reliability and longevity of electronic devices.
Curing Time
The curing time for RTV silicone can vary significantly, from just a few minutes to several hours, depending on the specific formulation and environmental conditions such as temperature and humidity. Rapid curing formulations can significantly boost production efficiency by reducing downtime and speeding up assembly processes. This flexibility allows manufacturers to select the appropriate RTV silicone based on their production schedules and requirements.
Operating Temperature Range
RTV silicone adhesives are designed to perform reliably within a broad temperature range of -50°C to 200°C. This wide operating range makes them suitable for use in extreme conditions, from cold outdoor environments to high-temperature industrial applications. Their ability to withstand such temperature variations ensures that the adhesives remain effective and durable, regardless of the environmental conditions.
Electrical Conductivity
The electrical conductivity of RTV silicones can be tailored to specific applications. Some formulations are electrically conductive, making them suitable for applications that require the creation of electrical pathways, such as in certain types of electronic circuitry. Conversely, other formulations are electrically insulating, ideal for preventing electrical shorts and protecting electronic components from electrical interference. This versatility allows RTV silicones to be used in a wide range of electronic and industrial applications, meeting diverse electrical requirements.
RTV Silicone Sealants
- Flexibility: Retains elasticity over a wide temperature range. This flexibility is essential for applications involving thermal expansion and contraction.
- Chemical Resistance: Resistant to water, chemicals, and UV radiation. This resistance ensures long-term durability in harsh environments.
- Adhesion: Strong adhesion to various substrates, including metals, plastics, and glass. This versatility makes RTV silicone sealants suitable for a wide range of applications.
- Curing Time: Similar to adhesives, can range from minutes to hours. The curing time depends on the thickness of the application and ambient conditions.
Differences Between Normal Thermal Adhesives and Sealants and RTV
Understanding the differences between normal thermal adhesives and sealants and their RTV counterparts is crucial for selecting the right material for your application.
Normal Thermal Adhesives and Sealants
- Curing Process: Often require elevated temperatures to cure. This can complicate the manufacturing process and increase energy costs.
- Flexibility: May become brittle over time and under extreme conditions. This can lead to cracking and failure in applications involving thermal cycling.
- Thermal and Electrical Properties: Generally lower compared to RTV variants. Normal adhesives and sealants may not provide the same level of performance in demanding applications.
RTV Conductive Thermal Adhesives and RTV Silicone Sealants
- Curing Process: Cure at room temperature, simplifying application and reducing energy consumption. This makes RTV materials more convenient and cost-effective to use.
- Flexibility: Maintain flexibility and elasticity, even in harsh environments. This ensures long-term reliability and performance.
- Thermal and Electrical Properties: Higher thermal conductivity and better electrical insulation, tailored for high-performance applications. RTV materials are specifically designed to meet the demands of advanced technologies.
Applications of RTV Conductive Thermal Adhesives and RTV Silicone Sealants
RTV conductive thermal adhesives and RTV silicone sealants are utilized in various applications, including:
- Electronics: For thermal management in CPUs, GPUs, and other high-power electronic components.
- Automotive: In engine components, sensors, and LED lighting systems.
- Aerospace: For sealing and bonding in aircraft and spacecraft components.
- Medical Devices: Ensuring reliable performance and safety in critical medical equipment.
RTV conductive thermal adhesives and RTV silicone sealants are used in a wide range of applications across various industries. Their unique properties make them suitable for critical tasks where performance and reliability are paramount.
Electronics
In the electronics industry, RTV conductive thermal adhesives are essential for thermal management. They are used to bond heat sinks to processors and other high-power components, ensuring efficient heat dissipation. This helps prevent overheating and extends the lifespan of electronic devices.
RTV silicone sealants are used for encapsulating and protecting sensitive electronic components from moisture, dust, and other environmental factors. Their excellent electrical insulation properties ensure the safety and reliability of electronic assemblies.
Automotive
In the automotive industry, RTV conductive thermal adhesives are used in various engine components, sensors, and LED lighting systems. They help manage heat generated by high-power automotive electronics and ensure the reliability of these components under extreme conditions.
RTV silicone sealants are used for sealing and bonding applications in engines, transmissions, and other critical systems. Their resistance to oil, fuel, and high temperatures makes them ideal for automotive applications.
Aerospace
The aerospace industry demands materials that can withstand extreme conditions and provide reliable performance. RTV conductive thermal adhesives are used for bonding and sealing components in aircraft and spacecraft, where effective thermal management is crucial.
RTV silicone sealants are used for sealing fuel tanks, windows, and other critical components. Their ability to maintain flexibility and adhesion under extreme temperatures and pressures ensures the safety and reliability of aerospace systems.
Medical Devices
In the medical device industry, RTV conductive thermal adhesives and RTV silicone sealants are used to ensure the performance and safety of critical equipment. These materials are used in diagnostic devices, imaging equipment, and other medical instruments where precise thermal management and sealing are required.
The biocompatibility and durability of RTV silicones make them suitable for medical applications, ensuring that devices perform reliably and safely over their intended lifespan.
Industries Served
RTV conductive thermal adhesives and RTV silicone sealants serve multiple industries, providing solutions that enhance performance, reliability, and safety. These industries include:
- Electronics and Semiconductors: For thermal management and encapsulation of electronic components.
- Automotive and Transportation: For bonding, sealing, and thermal management in vehicles.
- Aerospace and Defense: For sealing, bonding, and protecting components in aircraft and spacecraft.
- Medical and Healthcare: For ensuring the performance and safety of medical devices and equipment.
- Telecommunications: For sealing and protecting communication equipment and infrastructure.
RTV conductive thermal adhesives and RTV silicone sealants are invaluable in a variety of industries, each benefiting from their unique properties that enhance performance, reliability, and safety. Let’s delve deeper into how these materials serve different sectors:
Electronics and Semiconductors
- Thermal Management: In the electronics and semiconductor industries, managing heat is critical to maintaining the performance and longevity of devices. RTV conductive thermal adhesives are essential for bonding heat sinks to processors, GPUs, and other high-power components. These adhesives ensure efficient heat dissipation, preventing overheating and potential damage to delicate electronic parts.
- Encapsulation: RTV silicone sealants are used to encapsulate sensitive electronic components, protecting them from moisture, dust, and other environmental factors. This encapsulation not only provides a protective barrier but also offers electrical insulation, ensuring the safety and reliability of electronic assemblies. The flexibility of RTV sealants allows them to absorb thermal expansion and contraction, reducing stress on components.
Automotive and Transportation
- Bonding and Sealing: In the automotive industry, RTV conductive thermal adhesives and RTV silicone sealants are utilized for bonding and sealing various components. These materials provide strong, durable bonds that can withstand the vibrations and harsh conditions typical in automotive environments. For example, RTV adhesives are used to bond sensors, ensuring they remain securely in place and function accurately.
- Thermal Management: The high thermal conductivity of RTV adhesives is crucial in automotive applications where efficient heat dissipation is needed, such as in LED lighting systems and electronic control units. This thermal management helps maintain the optimal performance of these systems, extending their lifespan and reliability.
- Engine Components: RTV silicone sealants are widely used in engine components due to their resistance to oil, fuel, and high temperatures. They provide effective sealing in gaskets, preventing leaks and ensuring the smooth operation of the engine. The flexibility and durability of RTV sealants help them maintain their sealing properties under the extreme conditions found in automotive engines.
Aerospace and Defense
- Sealing and Bonding: The aerospace industry demands materials that can endure extreme temperatures, pressures, and environmental conditions. RTV conductive thermal adhesives and RTV silicone sealants are used for sealing and bonding applications in aircraft and spacecraft. These materials provide reliable performance in critical areas such as fuel tanks, windows, and structural components.
- Thermal Protection: In aerospace applications, managing heat is vital to prevent component failure. RTV thermal adhesives are used in thermal protection systems, ensuring that electronic components and other heat-sensitive parts remain within their operational temperature range. This protection is essential for maintaining the integrity and safety of aerospace systems.
- Flexibility and Durability: The ability of RTV materials to maintain their properties under extreme conditions makes them ideal for aerospace applications. They provide flexible, durable bonds and seals that can withstand the thermal expansion and contraction experienced during flight, ensuring the safety and reliability of aircraft and spacecraft.
Medical and Healthcare
- Device Performance and Safety: In the medical device industry, the performance and safety of equipment are paramount. RTV conductive thermal adhesives and RTV silicone sealants are used in various medical devices to ensure they operate reliably and safely. These materials are critical in diagnostic devices, imaging equipment, and other medical instruments where precise thermal management and effective sealing are required.
- Biocompatibility: RTV silicones are biocompatible, making them suitable for use in medical applications where contact with bodily tissues or fluids occurs. This biocompatibility ensures that RTV materials can be used in devices such as prosthetics and implants without causing adverse reactions.
- Sterilization Resistance: Medical devices often require sterilization, and RTV silicone sealants can withstand various sterilization processes without degrading. This resistance to sterilization methods, such as autoclaving, ensures that medical devices remain safe and effective for repeated use.
Telecommunications
- Sealing and Protection: In the telecommunications industry, RTV conductive thermal adhesives and RTV silicone sealants are used to seal and protect communication equipment and infrastructure. These materials provide robust protection against environmental factors such as moisture, dust, and temperature extremes, ensuring the reliability of communication systems.
- Thermal Management: Efficient thermal management is crucial in telecommunications equipment, where high-power components generate significant heat. RTV thermal adhesives are used to bond heat sinks and other thermal management components, ensuring that communication devices operate within their optimal temperature range. This management helps prevent overheating and potential failures in critical communication infrastructure.
- Durability and Flexibility: The flexibility and durability of RTV sealants make them ideal for use in outdoor telecommunications equipment, which must withstand environmental changes and physical stress. These sealants provide long-lasting protection, ensuring the continuous operation of communication networks.
Storage Guidelines
Proper storage of RTV conductive thermal adhesives and RTV silicone sealants is essential to maintain their quality and performance. Adhering to the following guidelines will ensure that these materials remain effective and reliable.
- Temperature: Store RTV materials in a cool, dry place with temperatures between 10°C and 25°C. Avoid exposing them to extreme temperatures, as this can affect their curing properties and performance.
- Containers: Keep the adhesives and sealants in their original, tightly sealed containers to prevent contamination and moisture ingress. Exposure to air can initiate the curing process, reducing the shelf life and effectiveness of the materials.
- Shelf Life: Adhere to the manufacturer’s recommended shelf life, typically ranging from 6 months to 1 year. Using materials beyond their shelf life can result in reduced performance and reliability.
- Handling: Avoid exposing the products to direct sunlight or high humidity. Store them in a well-ventilated area to prevent moisture buildup and ensure consistent curing properties.
Safety Measures
Handling RTV conductive thermal adhesives and RTV silicone sealants requires adherence to safety protocols to ensure user safety and product integrity. The following safety measures should be observed:
- Personal Protective Equipment (PPE): Wear appropriate personal protective equipment (PPE) such as gloves, safety goggles, and protective clothing to prevent skin and eye contact. Some RTV materials can cause irritation upon contact.
- Ventilation: Use RTV materials in a well-ventilated area to avoid inhaling fumes. Ensure that there is adequate ventilation to disperse any vapors generated during application and curing.
- First Aid: In case of contact with skin or eyes, rinse immediately.
Importance of Choosing the Right Thermal Adhesives
Selecting the appropriate thermal adhesive is crucial for ensuring optimal performance, longevity, and safety of the final product. The right adhesive provides effective heat dissipation, prevents overheating, and enhances the reliability of electronic components. Inadequate thermal management can lead to failures, costly repairs, and safety hazards.
In the world of electronics, thermal adhesive acts like a silent guardian angel. Choosing the right one is vital for a product’s success. Here’s why:
- Heat Dissipation Hero: Electronic components generate heat, and if not managed properly, they can overheat. Thermal adhesive acts like a heat bridge, efficiently transferring heat from hot components to cooler areas like heat sinks. This keeps things running smoothly and prevents components from cooking themselves.
- Overheating Nemesis: Inadequate thermal management is a recipe for disaster. Components that get too hot can malfunction, leading to product failure. This can be a major inconvenience for users and a costly headache for manufacturers.
- Reliability Rocket Fuel: By keeping components cool, thermal adhesive ensures they function reliably over a longer lifespan. This translates to happy customers with products that last, and less hassle for companies dealing with repairs and replacements.
- Safety First: Uncontrolled heat can pose a safety risk in extreme cases. Thermal adhesive plays a role in preventing this by maintaining safe operating temperatures.
In short, selecting the right thermal adhesive is an investment in the performance, longevity, and safety of your electronic product. It’s a small detail that can have a big impact.
Electo’s Trusted Products
At Electo, we offer a wide range of RTV conductive thermal adhesives and RTV silicone sealants tailored to meet the diverse needs of various industries. Our products are designed to deliver superior performance, reliability, and ease of use. Leading industries choose Electo for:
- High Quality: Our products undergo rigorous testing to meet industry standards.
- Innovation: We continuously develop new formulations to address emerging market needs.
- Customer Support: Our expert team provides comprehensive support and guidance.
At Electo, we pride ourselves on providing a comprehensive range of RTV conductive thermal adhesives and RTV silicone sealants that are meticulously engineered to meet the diverse requirements of various industries. Our commitment to excellence is reflected in the high quality, innovation, and customer support we offer, making us a preferred choice for leading industries worldwide.
1. High Quality
Quality is the cornerstone of our product offerings at Electo. Each of our RTV conductive thermal adhesives and RTV silicone sealants undergoes rigorous testing to ensure they meet and often exceed industry standards. Here’s how we ensure our products stand out in terms of quality:
Rigorous Testing
Every batch of our products is subjected to a series of stringent tests to verify their performance under different conditions. These tests include:
- Thermal Conductivity Testing: To ensure our thermal adhesives efficiently dissipate heat.
- Adhesion Tests: To confirm that our sealants and adhesives bond securely to various substrates.
- Durability and Flexibility Tests: To assess how our products perform under stress and over time.
- Chemical Resistance Tests: To verify that our sealants can withstand exposure to harsh chemicals and environments.
Compliance with Industry Standards
We adhere to international quality standards such as ISO 9001, ensuring that our manufacturing processes are consistent and our products are reliable. Our commitment to quality ensures that our customers receive products that perform reliably in critical applications, whether in electronics, automotive, aerospace, medical devices, or telecommunications.
2. Innovation
Innovation is at the heart of what we do at Electo. We understand that industries are constantly evolving, and so are the challenges they face. To stay ahead, we continually invest in research and development to create new formulations and improve existing ones. Here’s how our innovation benefits our customers:
Advanced Formulations
Our team of scientists and engineers is dedicated to developing advanced formulations that offer superior performance. For instance:
- Enhanced Thermal Conductivity: We have developed thermal adhesives with significantly higher thermal conductivity to meet the demands of high-power electronic components.
- Improved Flexibility: Our RTV silicone sealants are formulated to provide greater elasticity, making them ideal for applications subject to thermal expansion and contraction.
- Faster Curing Times: We offer products with reduced curing times to enhance production efficiency without compromising on performance.
Addressing Emerging Market Needs
By staying abreast of industry trends and technological advancements, we are able to anticipate and respond to emerging market needs. Whether it’s the miniaturization of electronic components or the increased demand for electric vehicles, our innovative products are designed to meet these evolving requirements.
3. Customer Support
At Electo, we believe that excellent products should be complemented by exceptional customer support. Our expert team is committed to providing comprehensive support and guidance to ensure our customers get the most out of our products. Here’s what sets our customer support apart:
Technical Expertise
Our support team comprises seasoned professionals with extensive knowledge of RTV materials and their applications. They can provide:
- Product Selection Advice: Helping customers choose the right product for their specific application.
- Application Guidance: Offering tips and best practices for applying our adhesives and sealants to achieve optimal results.
- Troubleshooting: Assisting with any issues that may arise during the application or use of our products.
Training and Workshops
We regularly conduct training sessions and workshops to educate our customers on the latest developments in RTV technologies and how to effectively use our products. These sessions are tailored to the needs of different industries, ensuring that our customers are well-equipped to leverage the full potential of our materials.
Ongoing Support
Our commitment to customer satisfaction doesn’t end with the sale. We provide ongoing support to ensure our products continue to meet our customers’ needs. Whether it’s answering a technical query or providing additional resources, we are always available to assist.
Why Leading Industries Choose Electo
Leading industries across the globe choose Electo for their RTV conductive thermal adhesive and RTV silicone sealant needs because of our unwavering commitment to quality, innovation, and customer support. Here’s why Electo stands out as a trusted partner:
Proven Track Record
Our products are used by top-tier companies in electronics, automotive, aerospace, medical devices, and telecommunications. These industries rely on Electo because of our proven track record of delivering high-performance, reliable solutions.
Customized Solutions
We understand that each application is unique, and we offer customized solutions to meet specific requirements. Our ability to tailor products to the precise needs of our customers sets us apart in the market.
Commitment to Sustainability
Electo is committed to sustainability and environmental responsibility. Our manufacturing processes are designed to minimize waste and energy consumption, and we continuously seek to develop eco-friendly products. This commitment not only helps protect the environment but also ensures that our customers can meet their sustainability goals.
Electo’s Trusted Products
At Electo, we offer a wide range of RTV conductive thermal adhesives and RTV silicone sealants tailored to meet the diverse needs of various industries. Our products are designed to deliver superior performance, reliability, and ease of use. Leading industries choose Electo for:
- High Quality: Our products undergo rigorous testing to meet industry standards.
- Innovation: We continuously develop new formulations to address emerging market needs.
- Customer Support: Our expert team provides comprehensive support and guidance.
At Electo, we pride ourselves on offering a diverse range of RTV conductive thermal adhesives and RTV silicone sealants, meticulously designed to cater to the multifaceted needs of various industries. Our commitment to superior performance, reliability, and ease of use has positioned us as a trusted partner for leading industries worldwide. Here’s a closer look at what makes Electo the preferred choice:
1. High Quality
Quality is the foundation of our product offerings at Electo. We understand that the reliability and performance of our products are critical to our customers’ success. Therefore, we have established rigorous quality control measures to ensure that every product meets the highest standards.
Rigorous Testing Protocols
To guarantee the highest level of quality, each batch of our RTV conductive thermal adhesives and RTV silicone sealants undergoes a series of comprehensive tests, including:
- Thermal Conductivity Testing: Ensures that our thermal adhesives can effectively dissipate heat, a crucial factor in preventing overheating in electronic components.
- Adhesion Strength Testing: Verifies that our products provide strong and durable bonds across various substrates, including metals, plastics, and glass.
- Durability and Flexibility Testing: Assesses how our adhesives and sealants perform under mechanical stress and over time, ensuring they retain their properties in harsh conditions.
- Chemical Resistance Testing: Confirms that our sealants can withstand exposure to a wide range of chemicals, oils, and fuels without degrading.
Compliance with Industry Standards
Our commitment to quality is further reinforced by our adherence to international standards such as ISO 9001. This certification ensures that our manufacturing processes are consistent, efficient, and continually improving. By adhering to these standards, we can guarantee that our products are reliable and perform as expected in demanding applications.
2. Innovation
Innovation is at the core of our operations at Electo. We are dedicated to staying at the forefront of technological advancements to meet the evolving needs of our customers. Our focus on research and development allows us to continuously introduce new and improved products to the market.
Cutting-Edge Formulations
Our team of experts is constantly working on developing advanced formulations that offer superior performance. Some of our innovative solutions include:
- High Thermal Conductivity Adhesives: Designed for applications requiring exceptional heat dissipation, such as high-power electronics and LED systems.
- Enhanced Flexibility Sealants: Ideal for applications involving significant thermal expansion and contraction, providing long-lasting seals without cracking.
- Fast-Curing Products: Formulations that reduce curing times, enhancing production efficiency and reducing downtime in manufacturing processes.
Anticipating Market Needs
By keeping a close watch on industry trends and technological advancements, we are able to anticipate and respond to emerging market needs. For example, the rise of electric vehicles has driven the demand for high-performance thermal management solutions, and we have developed specialized adhesives and sealants to meet these requirements.
3. Customer Support
At Electo, we believe that exceptional products should be complemented by outstanding customer support. Our expert team is dedicated to providing comprehensive support and guidance to ensure our customers achieve the best possible results with our products.
Technical Expertise
Our customer support team comprises highly trained professionals with extensive knowledge of RTV materials and their applications. They offer:
- Product Selection Assistance: Helping customers choose the right product for their specific application, ensuring optimal performance and reliability.
- Application Guidance: Providing best practices and tips for applying our adhesives and sealants to achieve the best results.
- Troubleshooting Support: Assisting customers with any issues that may arise during the application or use of our products, ensuring minimal disruption to their operations.
Training and Workshops
We regularly conduct training sessions and workshops to educate our customers on the latest developments in RTV technologies and how to effectively use our products. These sessions are tailored to the needs of different industries, ensuring that our customers are well-equipped to leverage the full potential of our materials.
Ongoing Support
Our commitment to customer satisfaction extends beyond the initial sale. We provide ongoing support to ensure our products continue to meet our customers’ needs. Whether it’s answering a technical query, providing additional resources, or offering on-site assistance, we are always available to help.
Customized Solutions
We understand that each application is unique, and we offer customized solutions to meet specific requirements. Our ability to tailor products to the precise needs of our customers sets us apart in the market. Whether it’s developing a new formulation to meet a specific challenge or modifying an existing product to enhance its performance, we work closely with our customers to provide the best possible solutions.
Commitment to Sustainability
Electo is committed to sustainability and environmental responsibility. Our manufacturing processes are designed to minimize waste and energy consumption, and we continuously seek to develop eco-friendly products. This commitment not only helps protect the environment but also ensures that our customers can meet their sustainability goals.
In concludion, Electo’s RTV conductive thermal adhesives and RTV silicone sealants are the products of choice for leading industries worldwide due to our unwavering dedication to quality, innovation, and customer support. By choosing Electo, customers gain access to high-performance materials that enhance their products’ reliability, safety, and efficiency. Our continuous efforts to innovate and provide exceptional support ensure that we remain at the forefront of the industry, ready to meet the evolving needs of our customers.
conclusion
RTV conductive thermal adhesives and RTV silicone sealants stand as integral components in modern manufacturing, holding a pivotal role in ensuring unparalleled performance and reliability across diverse industries. The selection of these materials is paramount, as it directly impacts the success and safety of products in various applications. At Electo, we prioritize delivering top-tier solutions that not only meet but exceed the highest industry standards. Our unwavering commitment to quality, innovation, and customer satisfaction positions us as a trusted partner for leading industries globally. By leveraging cutting-edge technologies and rigorous quality control measures, we ensure that our RTV products consistently deliver exceptional performance, resilience, and longevity. Whether it’s providing efficient heat dissipation in electronic devices, robust sealing in automotive components, or reliable insulation in aerospace applications, Electo’s RTV solutions are engineered to excel in the most demanding environments. With Electo as your partner, you can trust in our dedication to delivering premium-quality materials that elevate the standards of modern manufacturing and contribute to the success and safety of your products.
faqs (frequently asked questions):
What is RTV?
RTV stands for Room Temperature Vulcanizing, referring to a category of silicones that cure at ambient temperatures without the need for additional heat sources.
What industries benefit from RTV conductive thermal adhesives and RTV silicone sealants?
RTV materials find applications across various industries, including electronics, automotive, aerospace, medical devices, telecommunications, and more, due to their versatility and reliability.
How do RTV materials compare to standard thermal adhesives and sealants?
RTV materials offer distinct advantages such as room temperature curing, exceptional flexibility, durability, and resistance to environmental factors compared to standard thermal adhesives and sealants.
What are the storage guidelines for RTV materials?
RTV materials should be stored in a cool, dry place away from direct sunlight and sources of heat. Containers should be tightly sealed to prevent contamination and moisture ingress.
What safety measures should be followed when handling RTV materials?
When handling RTV materials, it is essential to wear appropriate personal protective equipment (PPE), work in well-ventilated areas, and avoid skin and eye contact. Disposal should be done following local regulations.
Why is it important to choose the right thermal adhesives?
Selecting the right thermal adhesives is crucial for ensuring optimal performance, reliability, and safety of products, as it directly impacts heat dissipation, adhesion, and overall functionality.
What makes Electo a trusted partner for leading industries?
Electo’s dedication to quality, innovation, and customer satisfaction, along with our premium-quality RTV solutions, positions us as a trusted partner for leading industries worldwide, ensuring the success and safety of their products.
How does Electo ensure the quality of its RTV products?
Electo is committed to meeting the highest industry standards by leveraging cutting-edge technologies, rigorous testing procedures, and continuous innovation to ensure that our RTV products consistently deliver superior performance and reliability.